For organizations to gain and maintain a competitive advantage, there’s a constant need for the…
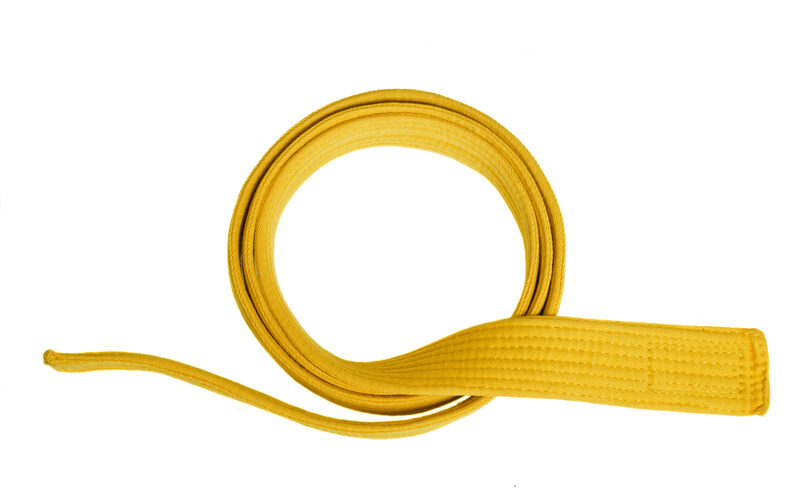
Being a Six Sigma professional is one of the best moves you can make for your career. Not only can it enhance the knowledge of your industry, but it can also open up new opportunities for career advancement. Six Sigma makes you a process improvement professional, which is a highly valuable thing for plenty of organizations in various industries.
However, there is no one Six Sigma certificate that encompasses everything it takes to be a process improvement professional. There are various levels or “belts” that signify to employers how well-versed you are with the methodologies and tools of Six Sigma.
To be one of these coveted professionals, you need to at least have a yellow belt. But what is a yellow belt and what do they do? Keep on reading to find out.
What is a Six Sigma Yellow Belt?
For anyone looking for an entry into the world of Six Sigma, being a yellow belt is the perfect starting point. This certificate offers foundational knowledge of Six Sigma. With this basic knowledge, they are able to assist other belts (green and white belts) during projects.
However, this does not mean that they can’t handle basic Six Sigma projects on their own. Sometimes, having a green and black belt can be overkill since all you need is a yellow belt with their basic understanding of lean tools and techniques.
An example of a Six Sigma technique that yellow belts know very well is the PDCA (Plan, Do, Check, Act) methodology. They understand this method and know exactly how to use it effectively in all projects they are assigned to.
What Is The Responsibility Of a Yellow Belt?
As you have now deduced, a yellow belt is responsible for assisting green and black belts in doing their job. Not only that, but they can also handle smaller and less complicated projects. But how do they do that?
As mentioned earlier one of the methods they need to know is the PDCA methodology. Other than that, here are other things the yellow belt should know to do their job effectively. Basically, a yellow belt must understand:
- Key concepts of Six Sigma, including how and why they were invented, as well as how they apply to their industry.
- The scope of the project and come up with a problem statement. A great tool that they can use in understanding the scope of the problem is SIPOC (Suppliers, Inputs, Process, Outputs and Customers)
- How to properly monitor a number of different processes. Should any of the processes malfunction, they should be able to work with the process owner to control the misbehaving process.
- Things from the perspective of the end-user or customer. This is because the end goal of every process is to deliver value to the end-user, who can also be a customer.
- The eight wastes. The wastes are transportation, motion, inventory, defects, overproduction, extra-processing, waiting and non-utilized talent. Only when they are removed can a process deliver maximum value to the end-user.
- Value Stream Mapping and Process Mapping in order to be able to visualize how processes deliver value.
- Data collection. Gathering, organizing and analyzing data should be second nature to yellow belts.
- Charts and how to create them using the data. Charts are an important part of analyzing a process to figure out how it can be improved. Charts to understand include Pareto Charts, Control Charts, Histograms and Scatter Plots.
- How to maintain processes and constantly improve them. Once a process is improved, a yellow belt’s job is not complete. It is up to them to find ways to improve them on a continuous basis and prevent them from misbehaving.
Conclusion
Six Sigma increases the value of employees in an organization. Even though being a yellow belt is a basic Six Sigma certificate, the role yellow belts play is extremely important in every project. From supporting higher belts to handling smaller projects, yellow belts are extremely valuable and one should not hesitate if they want to get this certification as an entry point into Six Sigma.
Comments (0)