Lean provides organizations in many industries a set of valuable tools for eliminating wastes in…
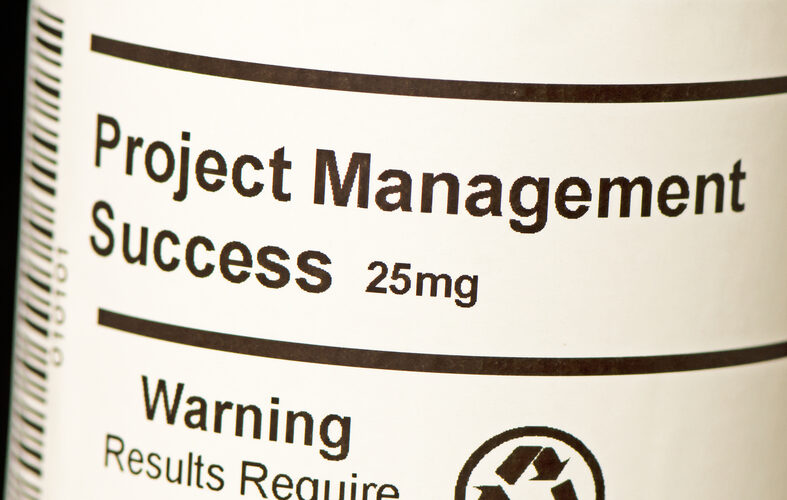
Six Sigma projects are meant to improve critical processes in an organization. If done right, this can yield positive results. This can be any number of benefits, such as financial gain and customer satisfaction. But the fact still remains that these Six Sigma projects need to be finished on time for the benefits to be realized.
This is why delays are a huge problem; not just for Six Sigma, but for any project. Knowing what can cause delays and how to solve them, means getting back on track and ensuring a successful Six Sigma project.
Here are five major problems that many black and green belts tasked with overseeing a Six Sigma project have run into and how they can be rectified.
1. The scope of the project is too big
When the scope of the project is too big, it can be difficult to meet assigned targets on time. This is one of the major causes of delays in a Six Sigma project. With deliverables being late and results taking too long to show, the project can lose support and steam.
To avoid this, the first thing that needs to be done is to make sure that the scope of the project is narrowed during the Define phase. Also, the project can further be divided into sub-projects, which can then be overseen by a number of black and green belts.
2. Belts don’t have enough time for the project
Six Sigma belts are usually employees of the organization in which the project is being undertaken. This means they still have to do their actual job on top of overseeing the completion of the project. They might get overwhelmed during the week to the point they relegate the project to after work hours and weekends, causing a delay.
For any Six Sigma belt working on the project, the supervisor should require them to schedule time during the week dedicated to the project. This means that during that time, their sole focus should be making sure their deliverables are on time.
3. Insufficient or no data available
Data is highly important in these types of projects. After all, how is one to know what the problem is in the absence of historical data? Furthermore, how are they supposed to figure out the root cause of the process inefficiency with little or no data to go by?
When there is little to no data available, the project can be delayed. This is because the belt is now tasked with the job of first collecting sufficient data and then working on the project. This is an entirely different project in and of itself.
The easiest way to solve this problem is to choose projects that have usable and sufficient historical data to work from. If not, the scope and the project can be redefined to work with the data gathered from the process each week.
4. Process owner resisting change
For a project like this to be successful, it needs all the support it can get. The most critical support should come from the owner of the process. However, many belts have found that the process owner is sometimes resistant to the improvement efforts, refusing to understand why the process needs improvements and how to improve it.
If a belt finds itself with a process owner that is resisting their efforts, it is up to the organization to educate the process owner and make them accountable.
Furthermore, they can make them sign a contract to make sure that they do all they can to help the belt do their job. However, the process owner should not feel like they will take sole blame for project failure (both process owner and belt are accountable).
Conclusion
For a Six Sigma project to be successful, knowledge of the delays and how to solve them can be vital to completing it. While there are many other problems that can cause a project to delay, these are the five biggest. Armed with this knowledge, black and green belts can make sure the project is on time.
Comments (0)