Lean provides organizations in many industries a set of valuable tools for eliminating wastes in…
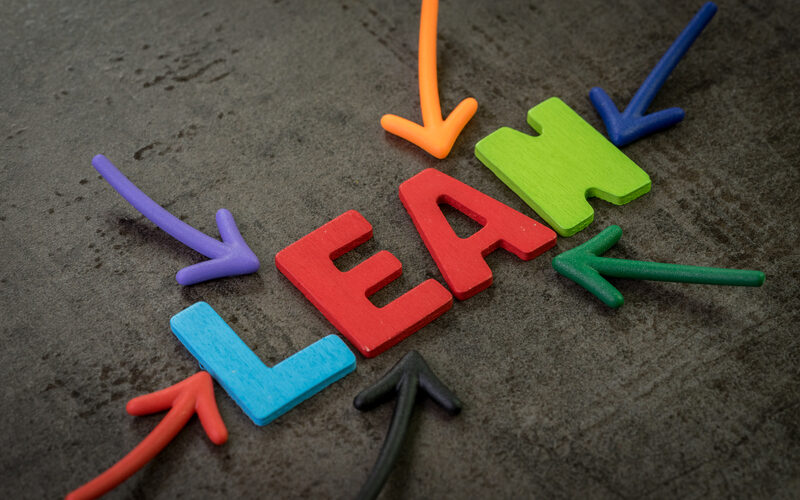
Giving customers what they need (value) by streamlining organizational processes and creating standardized workflows that are synced with real-time demand is at the heart of lean management. Through lean management, managers can identify value-adding steps in their organizational processes and improve or eliminate any step that is non-value-adding. That way, the managers can save a lot of valuable time and money, while making sure customer satisfaction is at an all-time high.
In order for lean management to be successful in an organization, there are five principles that managers need to know.
- Identify value – What does value mean to your customers? This should be clarified before taking any other step towards lean management. Basically, value is anything that customers find useful in solving a particular problem that they’re experiencing. You can’t do lean management without identifying what that thing is.
- Map the value stream – Every organization has a workflow, a series of repeatable steps that lead to an outcome. By mapping the workflow, managers can effectively visualize how value flows from the beginning of the process, through the supply chain and, finally, to the customer.
- Create continuous workflow – When the workflow is mapped, bottlenecks, which are things that interrupt the flow of value, are sure to be identified. Only by eliminating bottlenecks will value flow from beginning to end without interruption, creating a continuous workflow.
- Create a pull system – To ensure that nothing in the process goes to waste, there needs to be a pull system. With this system, work begins only when demand is available (e.g. a customer places an order). Without demand, no work is performed.
- Encourage continuous improvement – Once the above four principles have been put in place, the work has only begun. What was improved can always be improved further and so on. Plus, it is naive to think that once improvements are complete, other problems can’t arise. This is why everyone involved in lean management needs to also be involved in continuous improvement.
Comments (0)