A process map is a useful tool that helps you visualize all the steps in…
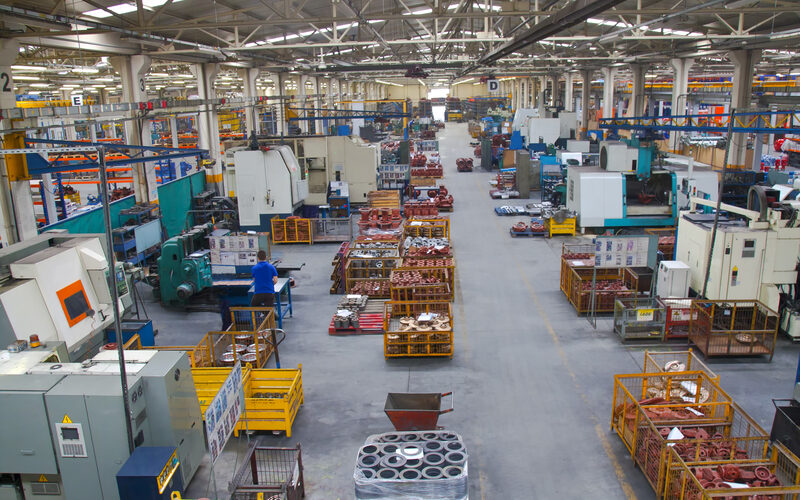
“We are going Lean!” These are the words that you will probably hear the first time your company decides to implement Lean manufacturing. Operating in a Lean fashion is a good first step towards perfection. Until now, many companies dealing with manufacturing has already applied Lean practices and achieved tremendous results.
What are those benefits of Lean Manufacturing?
Before we begin implementing Lean practices, there should be an understanding of the significant benefits that come with its implementation. As a matter of fact, it is not important that one company’s success will be the same as others, but the result, however, will be substantial. Moving ahead, here are some advantages of Lean implementation that industries should consider:
1. Waste Removal
The fundamental purpose of using Lean in any industry is to eliminate waste, which ensures advanced product quality. However, a complicated process can cause defects, which will further lead to a waste of time and a variety of other wastes as well. There are some Lean manufacturing tools such as Kaizen or TPM, which helps organizations remove any kind of waste from the process.
2. Quality Improvement
For a longer product life cycle, it is important for the manufacturing industry to improve upon the quality of the product. Well, the greatest number of benefits comes from Lean principles. A principle called ‘create flow’ can help the process flow down to every corner of the project. This balanced approach meets the production goals and delivers a top quality product keeping time constraints in mind. To successfully achieve the right flow, Lean Six Sigma practitioners use the tool 5S.
3. Cost Reduction & Revenue Generation
Using lean manufacturing, many organizations have learned the key to keeping inventory low by eliminating unnecessary stock. The control of inventory is equally important and Lean allows companies to cut down on supplies as per product requirement. This helps in saving a lot of money, for the organization to use for other purposes. Additionally, the product requirement technique is the reason behind some companies doing better as they always deliver their products and services on time. This, in return, generates great revenues and gives a boost to the business.
4. Employee Retention
If there is an error in the process, Lean practices hold employees accountable for tracking and rectifying that error. As the employees begin working on those errors, their involvement has risen to another level. This accountability culture empowers employees, which eventually increases the chances of employee retention.
In conclusion, though many manufacturing facilities have adopted the Lean culture, they are still far from it being completely deployed. It will obviously take many years of experience in Lean culture to be integrated into an organization.
Comments (0)