Lean provides organizations in many industries a set of valuable tools for eliminating wastes in…
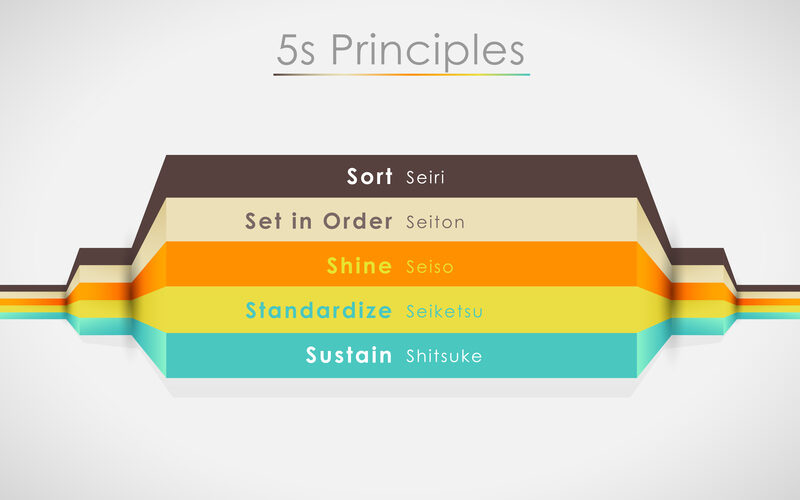
When Lean Manufacturing was introduced by Toyota Production System (TPS), they made it possible using a whole bunch of different tools. The tools are used in various functions as they serve various purposes. But one common goal for all the tools is to remove the non-value added activities (waste).
To successfully implement Lean practices, any facility will have to utilize certain tools. It is not mandatory to use all of the tools, but depending upon the workflow, you will have to choose the tools required by your organization. They play a major role in Lean transformation processes as they ensure efficient functioning and continuous improvement.
What is 5S?
For a successful Lean deployment, 5S has been one of the fundamentals tools. The need for 5S arises when there is a need to organize the work zone in order to keep it clean and safe. A neat workspace enables your creativity and productivity to function the right way.
The term ‘5S’comes from the Japanese language, where the letter S refers to the five different activities such as Seiri (Sort), Seiton (Set In Order), Seiso (Shine), Seiketsu (Standardize) and Shitsuke (Sustain).
1. Sort
Arrange your necessary and unnecessary items in two separate areas. The general idea is to have two spaces, one to keep items that you need and other for things you don’t need anymore. And then get rid of unnecessary items in order to create more space for important items.
2. Set In Order
Creating a visual of necessary and daily used items can enhance your creativity. Keep frequently used items in a logical order to help you reach those items without any hindrance.
3. Shine
The third step involves cleaning the work area, checking for any leakage in all the machinery and equipment and if found, make sure to remove it. This technique ensures the elimination of any disintegration of equipment to arise in the future.
4. Standardize
While performing these steps, pick the best practice out of all and standardize it. A standard of procedures is crucial to keep the sustainability alive.
5. Sustain
Many organizations apply these steps and achieve tremendous results, but they fail to sustain the process and eventually fall back into the pit. Always ensure to sustain the workflow utilizing the set of standard procedures mentioned above.
This process will end up giving you more room for important equipment, saving time and helping eliminate excess inventory.
Comments (0)