Lean provides organizations in many industries a set of valuable tools for eliminating wastes in…
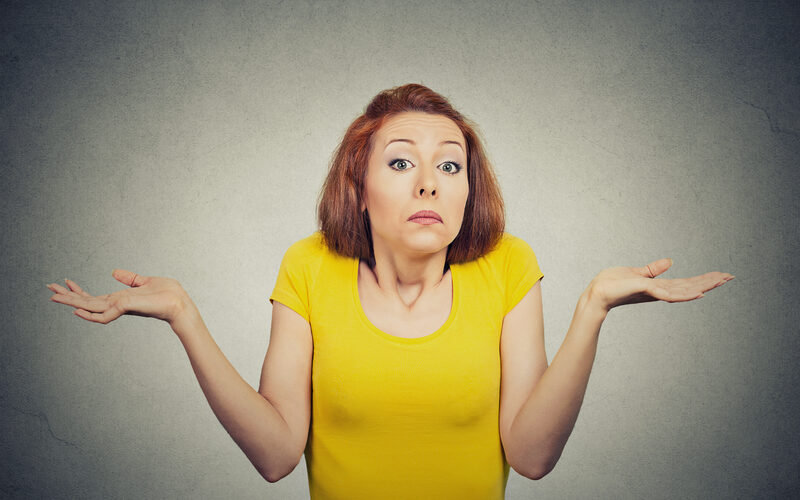
Lean is a business methodology, which removes waste and improves quality through a set of tools and techniques. Although Lean has been a successful methodology, business practitioners have their doubts. But before forming these opinions, we advise to have a little more understanding of Lean processes and then decide for yourself. Do you also have Lean misconceptions? Let us help you bust those misconceptions.
When Toyota first implemented Lean in their manufacturing process, the methodology proved its worth, resulting in much success for the company. Because of that success, the company decided to implement Lean in other functions such as sales and human resources and the results were almost the same, brilliant! Lean has come a long way ever since, with big brands like Ford and Honeywell coming on board. Despite so many industries using Lean, there are still some misconceptions about it, which may cause some obstacles.
These few common Lean misconceptions should help clear up the definition of Lean:
Lean is not going to work for other industries because it was initially developed for manufacturing.
No, any tools and techniques of Lean with a little modification based on a business practice works smoothly for any function or industry. Lean can be easily implemented in any organization. The combination of lean methods and internal changes within each organization can make a difference.
Lean is expensive and will eat up valuable time.
At first, every methodology will be time-consuming because every employee has to learn its way through it. Lean requires full attention and commitment to reach the goal. After a successful implementation, it becomes an easy standard to follow. Lean may require a large investment up front, but the additional revenue generated to make it worth the time and money.
Lean means more work and fewer employees.
The many powerful tools and techniques of Lean implementation help in process improvement whereas the idea of fewer employees requirement is just a common misunderstanding. In most cases, reducing staff size may ultimately make the Lean process fail. Lean, however, does reduce the workload and frees up time for the employees to fill it up with other tasks.
Comments (0)