There is something wrong with your process: it keeps failing and you don’t know why.…
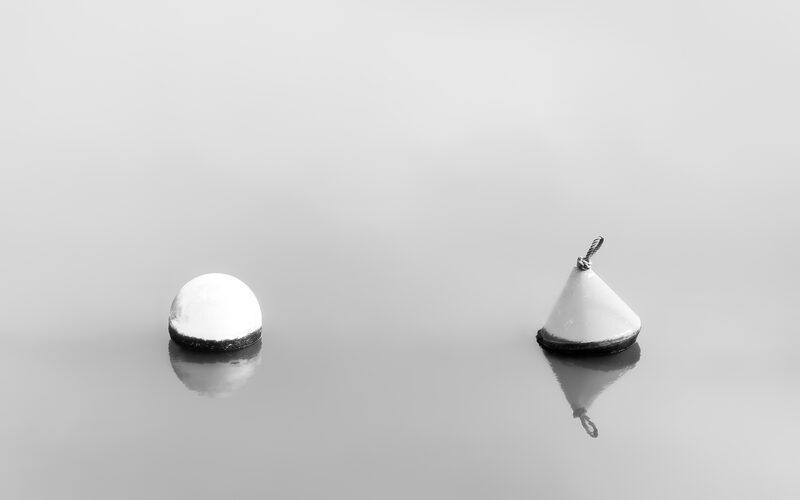
In understanding the practice of Six Sigma, one of the first things to understand is the distinction between various techniques and principles. There are two principles of Six Sigma – DFSS and DMAIC, which are crucial for the success for Six Sigma’s deployment. Let us learn a little about the differences between these two principles.
DFSS (Design for Six Sigma) is responsible for the creation of new products or business processes which can possibly replace the old ones in any industry. To create a new product, there should be an evaluation of existing products. Also, this new product will have a greater efficiency and its efficiency level has to be at least 4.5 sigma. Additionally, the development of a new product depends on any of the following cases:
- If a product fails to meet the customer’s specifications.
- The performance of the product has degraded.
- The product is beyond repair or improvement.
Now, How exactly do DFSS and DMAIC differ? Let’s find out.
DFSS and DMAIC
DFSS is a methodology used for product development, but DMAIC is more inclined towards the establishment of continuous improvement. The two techniques serve almost the same purposes, yet they have different approaches. Not to mention, the goal of both the techniques is to have customer satisfaction. The only difference is that the DMAIC approach tends to analyze the product and improve it with time, whereas DFSS comes into picture when all the possible improvements are done and the customer demands are yet not fulfilled, so the development of new product begins.
Let’s learn about DMAIC first because to understand DFSS, we have to know how DMAIC works as it is the primary approach. So, what phases are involved in DMAIC? Find out here:
1. Define
This is the phase where we identify the problem and define business objectives. Another process is to review customer requirements and create a team for better engagement (Tools can include: Project Charter, SIPOC, etc.).
2. Measure
The second phase is to collect the relevant data and validate the measurement system to comprehend the problem (Tools can include: Data Collection Plan, VSM, etc.).
3. Analyze
An ideal practice of this phase is to do the analysis of data through a meticulous process of discerning the root cause of the problem called RCA (Root Cause Analysis) (Tools can include: Data Analysis, Process Analysis, DOE, etc.).
4. Improve
Next, for process improvement, the right way is to acknowledge the problems and finally eliminate those. This step involves solution generation, its selection, and implementation (Tools can include FMEA, etc.).
5. Control
In the final step, Six Sigma practitioners always control the process for it to continuously improve. To put it another way, the process may suffer a little due to abrupt changes. This is exactly why sustainability is important. So, keep monitoring your processes to ensure there are no errors in the future (Tools can include: Control Plan, Control Charts).
To understand how the DFSS technique works, we should know more about the DMADV (Define, Measure, Analyze, Design and Verify) technique. DMADV is nothing but a technique used for DFSS. In DMADV, the first three steps are exactly the same as the DMAIC approach, except for the last two steps.
When we begin implementing DMADV, we start the same way as DMAIC and then when it comes to the last two steps; we should follow these:
4. Design
After the third phase of analyzing the process, if we find the product is beyond any improvement, it’s finally time to develop a new one. For this, take a customer’s input (maybe using a feedback) and design a new product that suits the customer needs.
5. Verify
Furthermore, when we have finally developed the new product, it’s time to finally verify its effectiveness and perform all the quality checks on it.
To conclude, the two approaches are great initiatives to achieve organizational goals in terms of product quality, life cycle, and many others. Besides, these results bring positivity among employees and encourage them to implement these approaches as much as possible. Have you tried these already? Let us know in the comments about the challenges you faced.
This Post Has 0 Comments