Lean provides organizations in many industries a set of valuable tools for eliminating wastes in…
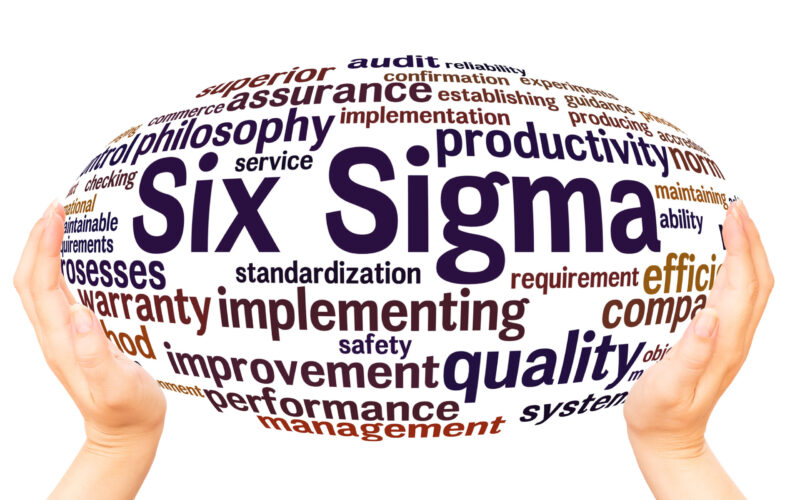
Lean is all about eliminating waste in organizational processes and Six Sigma is about reducing variation (unexpected results or defects). Lean and Six Sigma, although distinct, go well together. They provide a massive competitive advantage to organizations that want to deliver value on a consistent basis.
Any organization that wishes to take advantage of Lean Six Sigma needs to know the following five principles.
1. Keep the Focus on the Customer
Any improvement you wish to make should add value to the organizational processes. In this context, value is defined as anything that the customer is willing to pay for. Identify the demands of your target customers and use them to drive your processes.
2. Identify Problems to Focus On
When improving a process, you need to look at all the steps and identify the problems therein. And when you find the problems, use a data-driven approach to identify the root causes. That way, you don’t waste time on surface issues that do little-to-nothing to eliminate the problems at hand.
3. Eliminate Anything that Doesn’t Add Value
With the root problems identified, you will know exactly what is leading to waste and variation in the process. By eliminating them, you will be left with only those steps in the process that provide value.
4. Communication with Team Members
With the processes running efficiently, it is time to communicate the changes made with the entire team. This will ensure that people don’t go back to doing what led to waste and variation in the first place. It is vital to train all members on any new procedures to make sure the change sticks.
5. Embrace Change and Be Flexible
People are resistant to change, and Lean Six Sigma brings a lot of change with it. Not only should you embrace change, but your employees should be encouraged to embrace it as well. This is by no means an easy task, but it is critical to the success of Lean Six Sigma.
Comments (0)