Lean provides organizations in many industries a set of valuable tools for eliminating wastes in…
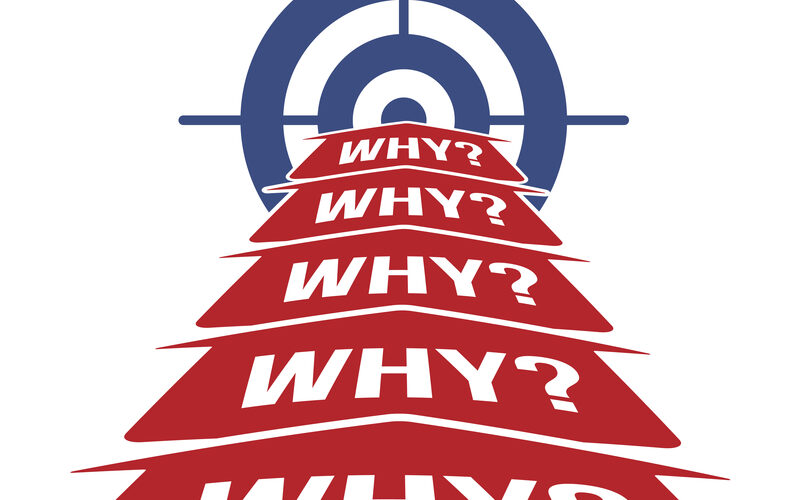
The 5 Whys is a technique or process where a set of iterative questions are asked multiple times until the root cause of the problem is determined. A root cause of a problem can be found deep within a process, which can cause harm to the organization’s behavior depending on that particular process. In most cases, the problem is introduced to the organization by a customer or client who encountered the problem when he started using that particular product. To rescue the organization from such a situation, the process ‘5 Whys’ can be an effective tool.
To determine the root cause, few questions are more than enough whereas the ideal number is five. Usually, five questions are more than enough to discern the root of the problem, and so the name ‘5 Whys’ was given to this process.
The 5 Whys is a very common method to get to the basics to find out the ultimate root cause. It is highly effective if performed appropriately. Some managers may perform it in a very generic way, which leads them nowhere close to the solution.
Hit the Right Nerve and Ask the Right Questions
Generally, people just rectify the ongoing issue for the sake of dealing with it. The ideal way to perform 5 Whys is to ask very specific and solution-based questions. Generic questions such as “Why did the process fail?” or “Why hadn’t anyone noticed it any sooner?” won’t be of much help.
“The process failed because the members didn’t pay attention to product variation,” is not the kind of answer you should be looking for. The idea is to tweak the problem and discern appropriate solutions.
The best part about this process is that it is applicable everywhere. It’s not necessary to have a Lean Six Sigma methodology involved to make use of the 5 Whys. Since this tool is easier to use, we advise to use it in your day-to-day activities as well.
Comments (0)