Lean provides organizations in many industries a set of valuable tools for eliminating wastes in…
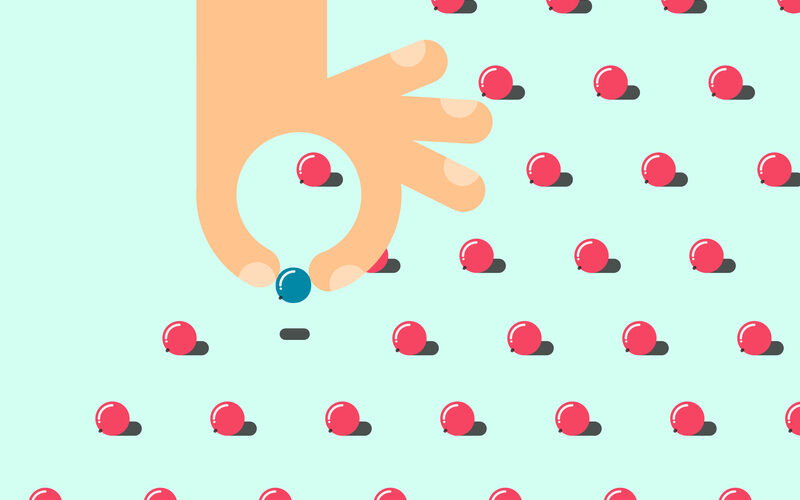
During the course of our business careers, we all try to strive for perfection in our tasks. And if you’ve ever tried to get your hands on Six Sigma, you probably have gotten the chance to learn about the term zero defects. The general idea of implementing zero defects is less waste, fewer errors and defects, and a significant increase in revenues.
Now, this concept is debatable in quality standards, as some may regard it as an idea where perfection exists; and there’s no room for improvement in a business process. But others may shun it as a concept which is highly unachievable and may even call it an illusion. As for us, we say the idea varies as per the business project or process. And it also depends on the stages of the project – whether that’s the beginning or implementation stage.
Before we go any further,
Let’s have a look at some questions to think about after the idea of implementing zero defects is seeded:
- How many errors and defects do we have?
- How do we reduce them?
- How do we prevent these errors in the future?
And the ultimate question,
How do we achieve zero defects or perfection?
Although you may need to put more of your time to this through an intense learning of Six Sigma, here are our two cents on this concept of achieving perfection:
- It would be illogical to say that zero defects will bring immense success and give you flawless results because no process can ever be defect free. There would always be a need to fix one or other things. But it clearly doesn’t mean that zero defects has to be a concept that one can easily refute as another technique that just won’t give positive results.
- The concept of zero defects has a few kinds of variations, which enables its application in multiple areas in multiple ways. It’s not unknown to any of us that errors differ from each other in different processes. Some errors may need an immediate action and some may turn out to be tolerable enough for a longer time. Of course, there’s no way that we would tolerate any kind of error or defect, but it’s about priorities. It may come to your attention that certain other errors need prompt action over the rest.
- Another notion of zero defects is that it is an act of attempting things right the very first time. This impression of zero defects allows anyone to use the technique in each corner of the business. And it goes further to an extent where if things are done right the first time, they will sustain and eventually bring us spectacular results.
In conclusion, our final opinion is this: Yes, zero defects is possible to achieve, but only in certain areas of business. Not every process is capable of achieving perfection.
Comments (0)