Lean provides organizations in many industries a set of valuable tools for eliminating wastes in…
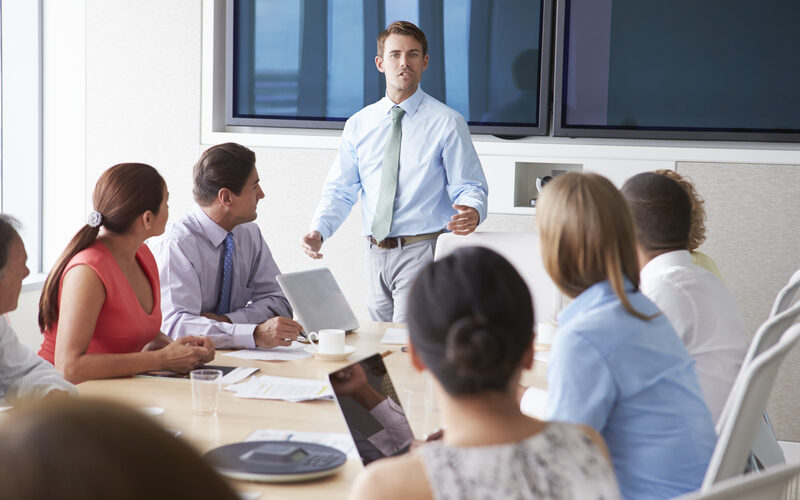
In an organization, some of the important elements of a process aren’t measurable enough. They may be hiding under the ground. So, to unravel these processes, a practice called the Gemba walk was conceived. Gemba, in Japanese, means “the real place.”
In lean manufacturing, it takes place on the shop floor, which one could consider the heart of the company, where many of the central functions take place.
A Gemba walk is a great tool to discern the non-measurable elements, which are causing critical harm to the business. This tool ensures a strong observation of processes that work and the ones that don’t. This way certain processes can’t be overlooked by management. In fact, the concept of this walk is to do a pertinent analysis of the shop floor and take necessary measures to enhance the processes.
How to Perform a Gemba Walk?
To efficiently practice this walk, leaders and managers always let continuous improvement have a hold over the processes. Other than that, the employees at an authority level, such as team leaders, managers, and supervisors, usually perform this walk. How does it work? How do you perform an extremely efficient Gemba walk? We give you a few tips to carry out a productive Gemba walk:
- Before starting a Gemba walk, having a discussion with other leaders to set perspective on the business situation will help in prioritizing the achievable outcomes.
- During the walk, have a thorough analysis of Gemba, look for anomalies, and see if employees’ goals align with the company’s motto or purpose.
- Understand the real purpose of the employment of this walk, which is to bring the key issues to light.
- The frequency of this walk is the decision of a manager or a leader depending on the situation.
To keep consistent improvement, it becomes necessary for companies to keep practicing the Gemba walk. The many advantages of a Gemba walk involve process enhancement, consistent goal alignment, reduced cost of quality and increased employee productivity.
Comments (0)